Are you still worried about our quality problems? Let's see how we can control the quality.
- Share
- Issue Time
- Feb 26,2019
Summary
Tell you the QC (Quality Control) steps in our factory throughout the whole make process from when the garment is gone from SMS being 100% sealed to a PPS being made and confirmed to full production being made. How many inspection points we have throughout the stages and is there a final measurement to work out if the garments are within the tolerances we set?
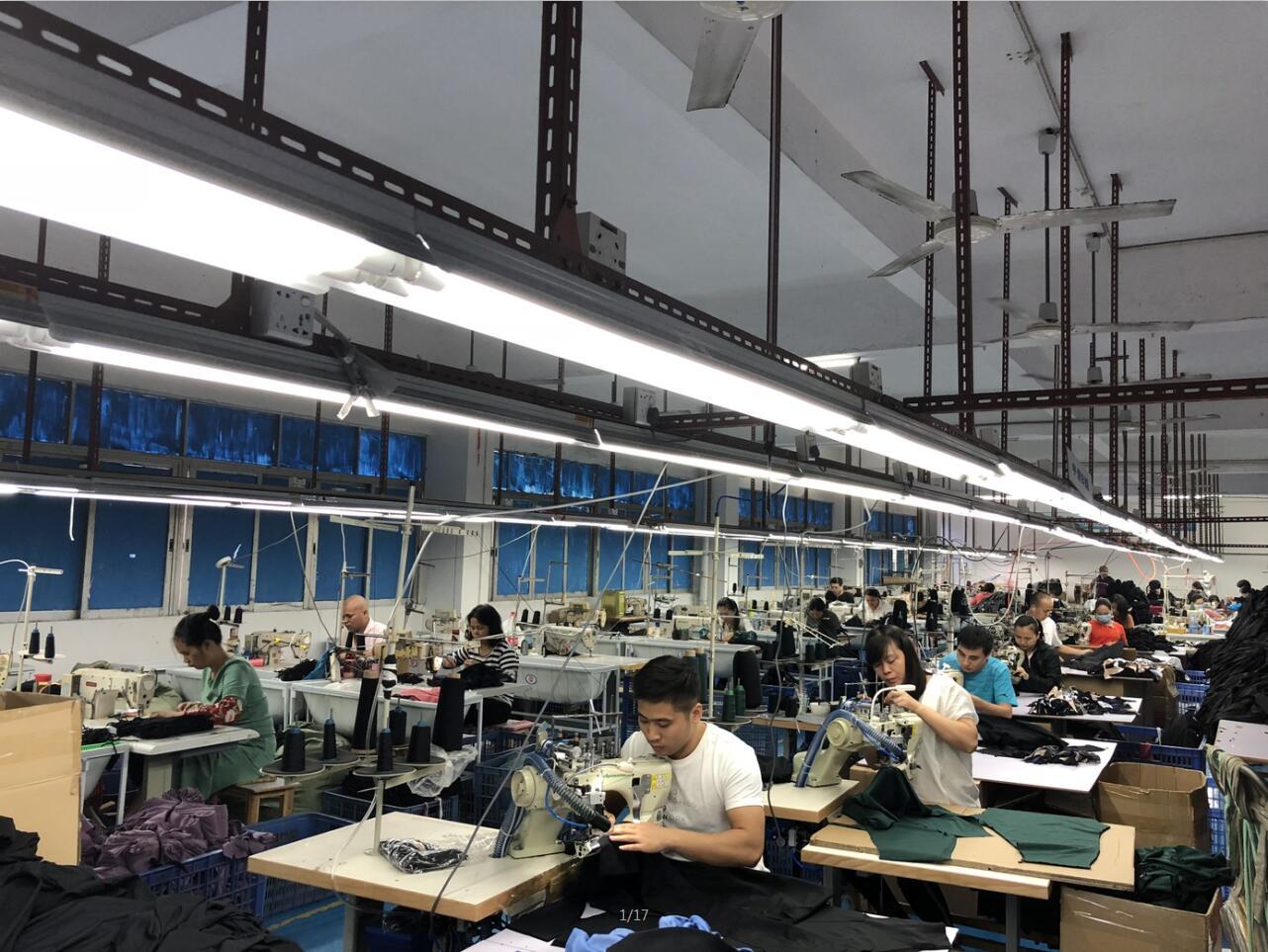
Many first-time customers, more or less, are concerned about our quality control.
Next, tell you the QC (Quality Control) steps in our factory throughout the whole make process from when the garment is gone from SMS being 100% sealed to a PPS being made and confirmed to full production being made. How many inspection points we have throughout the stages and is there a final measurement to work out if the garments are within the tolerances we set?
QC (Quality Control) steps:
1. We purchasefabric from our fabric suppliers, then we will check the fabric quality frist then carry fabric to be preshrunk.
2. About sizing, before we cut the fabric, we will provide size sheet for you to confirm, after you confirm full sizes, we will grade and make full size paper patterns.
3. In the mean time, we will make pre production samples which same as the one we sent youor make the changes which you require. Whole mass production will follow the size sheet and PP samples.
4. Printing and embroidery: before we start mass printing or embroidery, our printing and embroidery suppliers will provide us pre production samples to confirm first. Wewill check them and wash printing. Once we confirm. They will follow the PP samples to start mass printing and embroidery. When all printing and embroidery be finished, they will be sent back to us, then our production manager and oursellers will check them again.
5. Stitching: even if simple leggings need several kinds stitching methods and different workers make different stitchings. Before the start mass stitching, they will stitching several pieces first then provide to our production manager, she will check the quality, if the stitching is not good, she will teach them how to make it better. During whole stitching process, our production manager will check the stitching quality several time and measure the size. But just random inspection not inspect every single one.
6. When the clothing finished stitching, will be move to another floor. Then we iron and packing there. Sometime some stitching problems will be found when ironing, for example the bottom edge of jackets. No matter how hard you iron the edge can not be even, this is stitching problem. If we found these problems, the clothes will be returned to stitching workshop to be fixed. After ironing, we will check every single clothing quality. and measure the size randomly.
7. When we packthe clothing, as long as the packing workmates find some problem. They will take these clothes out.
Above all, I believe you are quite comfortable with the quality of our products. If you have business needs, please contact us.
Contact information:
E-mail: admin@hcsportswear.com
+8613602338395